Published: August 2nd 2016
Despite many attempts and different solutions for controlling dust over the years, dust is still an ongoing problem for companies using conveyor belts to move material. Because different methods of dust control greatly vary, material handlers need to research how processes and techniques affect their specific conditions to accomplish the best approach for their operation.
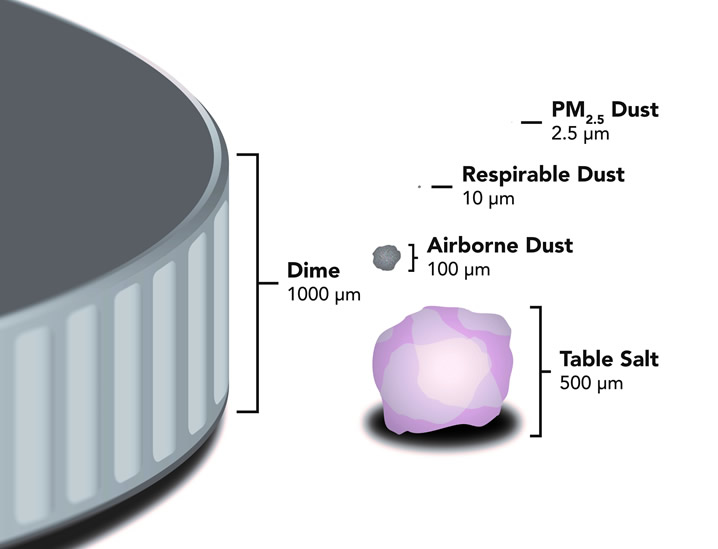
Normally, the focus is placed on smaller dust particles (100 microns or less [.004”]) as they tend to stay airborne while larger, heavier particles usually settle out of the air.
Suppression VS. Prevention
Suppression and prevention are commonly debated when it comes to dust control methods. Suppression involves treating the dust once it has been released from the material stream. In comparison, prevention requires influencing the particle size, cohesion and/or air velocity before dust is created, typically using a physical or chemical treatment of the transported material.
Before specifying a solution, the user must consider which approach is more suitable for their specific material and process. Is the objective to prevent the dust or control it? If prevention is the preferred solution, adding moisture is the most common, increasing both particle size and cohesiveness. This water can be added in numerous ways, but the important question is: how much moisture can the material endure?
A unanimous answer does not exist. Every process, every material, even different loads of the same material, can display different properties. Adding a known percentage of moisture may be an effective solution at one site while a relatively minor fluctuation could have negative consequences such as thermal penalties or quality loss at another site.
Testing
Aiding customers in calculating the effects of specific amounts of moisture on dust, Martin Engineering’s Center for Innovation (CFI) developed a dedicated test apparatus and process. The test setup consists of a vibratory feeder dropping material a known height into a spinning hopper. When the material falls, it creates dust, which is contained under an airtight transparent thermoplastic hood. Attached to this hood is a vacuum blower to pull all the air and dust from inside the enclosure through a 3-micron filter.

Filtered outside air is taken into the enclosure to create a flow. The blower and openings are large enough to capture all of the dust before it can settle but not so large as to actually hinder the material stream. The filter element is weighed before and after the test to establish the actual amount of dust produced. The weight is then used to find the percentage of dust created out of the entire mass of the sample.
To test the process, a sample was taken from a material stream at a power facility using Powder River Basin coal. Again, the sample was weighed, dried and weighed again to determine the moisture content when it arrived. The sample was mixed to guarantee uniform consistency and then broken into several test samples of approximately 1 gallon (3,785 cm³) each. These samples were combined with water to produce varying moisture contents, then each was blended in an identical fashion to guarantee undeviating water distribution.
Each sample was weighed and placed into the dust chamber. The material was agitated, dust was created and the amount of dust captured in the filter was weighed. The airflow, feed rate and drop height were held constant between tests. For comparison, the same procedure was conducted at a second facility, burning similar coal. This second site was only 200 miles from the first, but the environment, material and process were different.

Also, there is a moisture level at which the material becomes saturated, and dust is no longer produced. In these examples, this point is around 30% moisture content for application 1 and 15% for application 2. Adding additional water beyond this concentration has no benefit.
Even though similar materials were used, the amount of potential dust is different from site to site. The coal in application 2 is much more sensitive to the addition of water to prevent dust. This determines the same basic material, from a source just 200 miles away, has different properties, reinforcing the need for site-specific testing and solutions suited specifically to the individual application requirements.
If an existing material handling system works upon installation, it should continue to work as long as the material stays constant and the equipment does not suffer wear or abuse that changes its performance.
Surfactants and Foams
If plain water isn’t adequate to control the dust, or if the material reaches the highest level of allowable moisture content before adequate control is achieved, a surfactant can be added to improve spreading and bonding. While a plain water system may require only water or possibly water and electricity to power a pump, adding a surfactant demands both water and electricity, as well as the cost of the chemical. The more components there are to a dust control system, the greater the expense.
Moisture can also be added in the form of foam. In addition to its surfactant properties, foam physically expands the moisture, so a smaller amount of water can be used to treat the surface material. A foam system is typically even more expensive, as it requires four elements: water, electricity, compressed air and the foaming agent. While the cost is greater, it can deliver effective results with far less moisture than a plain water spray or water-surfactant system
Conclusions
No two materials are the same, no matter what. Every conveying system will have its own individual characteristics. It is essential to examine the features, construction and trouble points of their systems, without making assumptions that could lead to disappointing outcomes.
Experienced material handling equipment manufacturers often have complex testing facilities to examine the material’s physical properties. Physical testing of a bulk solid is important to the proper design of material handling systems. The cost of testing is a minor part of the overall expense of a conveying system.
The one thing that all materials have in common is a minimum and maximum moisture content for dust suppression. While the values for any two materials will not be identical, all materials can (and should) be tested to determine the effective range for added moisture, identifying the percentage of water content needed for optimum control of each specific material being conveyed.