Product Types Used | Belt Cleaning Solutions , Primary Belt Cleaners , Secondary Belt Cleaners |
---|---|
Industry | Mining |
Customer | A plant in Rio de Janeiro, Brazil |
Problem

A large Brazilian mining company was experiencing serious carryback issues on conveyors hauling iron ore to its ship loader lance. The operation processes ~65 million tons of ore annually at two sites, using a total of 38 conveyors that range in size from 48" to 72" (121.9 cm - 182.9 cm) and run at 4.5-5 m/s (14.8 f/s - 16.4 f/s). The existing spring-tensioned belt scrapers were unable to effectively remove adhered cargo, causing extensive spillage that presented a potential safety hazard and required regular cleanup of the heavy, tacky cargo. The fugitive material also adhered to rollers and other moving parts, resulting in premature equipment wear, increased downtime and higher operating expenses.
Solution
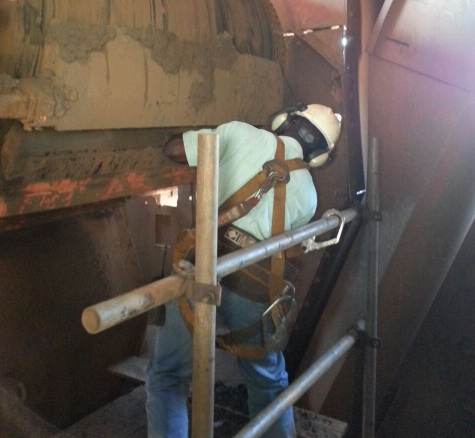
Martin Engineering technicians performed an audit on the conveyor to assess the problem and determine a solution. They concluded that the operation was a good candidate for the company's new Automated Blade System (ABS), an automated pneumatic tensioning system for belt cleaners. The new design from Martin Engineering delivers precise monitoring and tensioning throughout all stages of blade life, improving cleaning performance and reducing the labor typically required to maintain optimum blade pressure and maximize the service life of both the belt and the cleaner blades.
Result
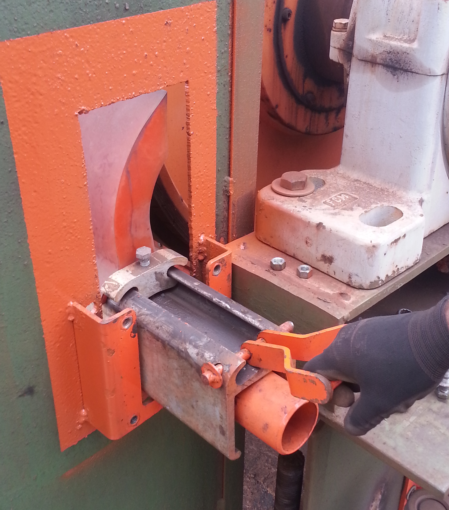
The results were quickly apparent upon installation of primary and secondary belt cleaners using the new tensioning system. Carryback and spillage have been drastically reduced, preventing thousands of tons of lost material. Operators report longer belt and component life, reduced maintenance time and improved safety. "The pneumatic belt cleaners give us reliable stability," said the Maintenance Manager. "Operators have reported no issues with the self-adjusting cleaners, and we already have plans in place to install additional units during the coming year."