Products Used | Impact Cradle MD |
---|---|
Product Types Used | Transfer Point Solutions |
Industry | Steel |
Customer | Tata Steel Ltd. |
Problem
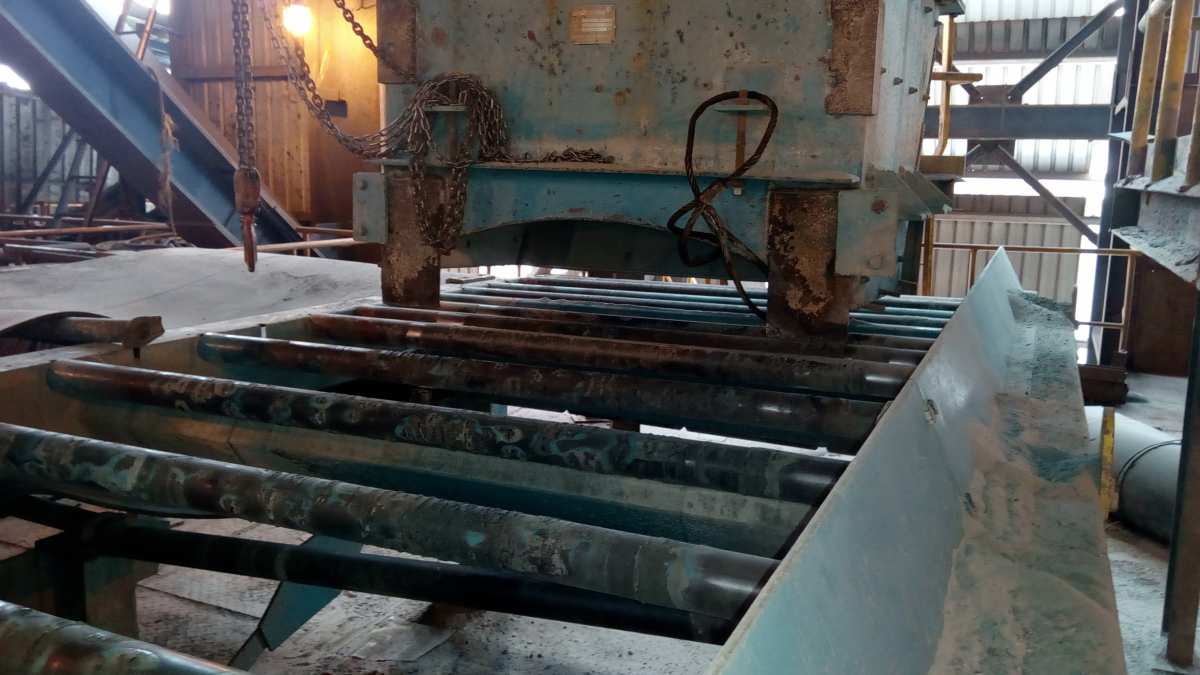
The Tata Steel Ltd. plant in Eastern India with an annual production capacity of 3 million m/t (5.5 mil. s/t) was experiencing equipment damage on one of the main conveyor transfer points due to high-weight material impact. Loading onto a 1220 mm (48 in.) wide belt with an unobstructed vertical descent, fines would collect on the walls of the transfer chute and the weight would cause them to dislodge from the wall. Large chunks impacting the belt at a high momentum would bend impact idlers and damage bearings. This resulted in seized idlers, leading to belt wear and frictional heat, a potential workplace hazard. Quarterly, downtime for 8-9 hours was needed so workers could replace frozen impact idlers and maintain a safe work environment.
Solution
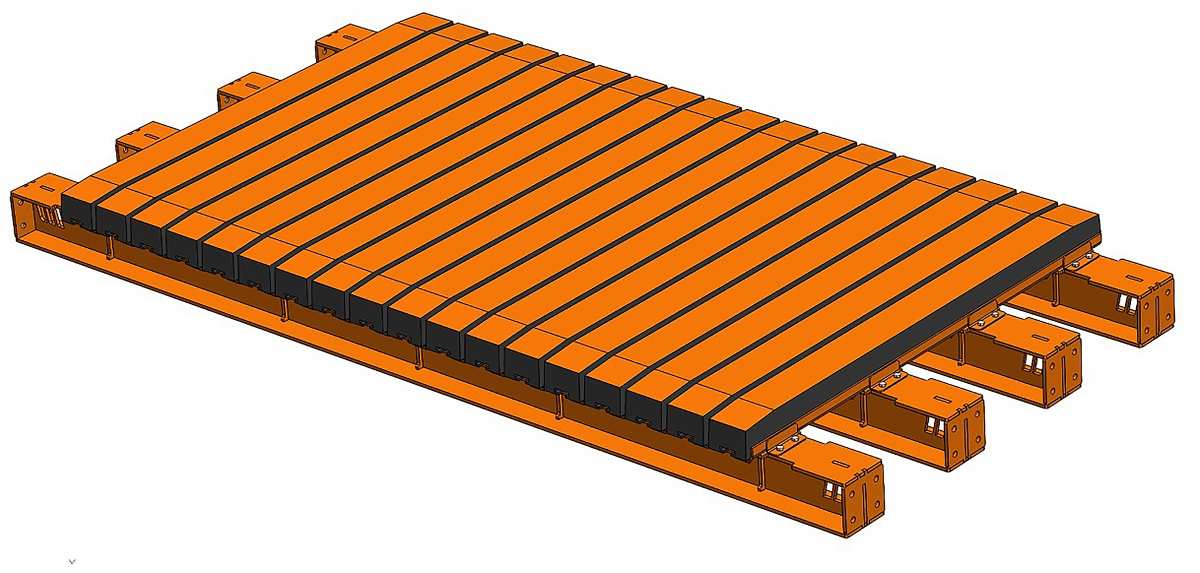
Representatives from Martin Engineering India were invited to examine the issue and make recommendations. Based upon the weight of material, volume and height of the transfer chute, technicians replaced the existing equipment with a Martin® Impact Cradle MD (Medium Duty). Installed under the belt conveyor loading zone, the unit has 18 rugged energy-absorbing urethane bars with a top layer of low friction UHMW polymer, which produce very little belt wear. Laid flat to conform with the design of the existing system, the 75 mm (3 in.) thick, 1220 mm (48 in.) long impact bars absorb the force to prevent damage to the belt and structure. The bed of reinforced steel is affixed to the mainframe for extra support, meeting all CEMA design standards.
Result
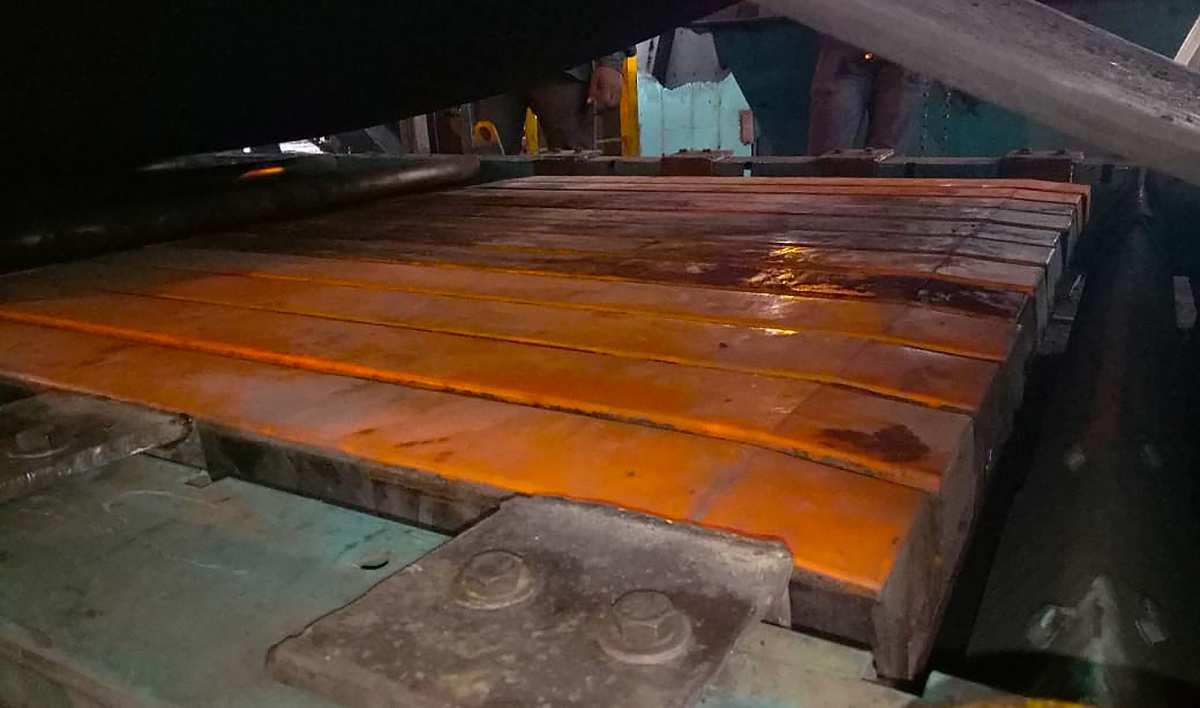
Nearly a year and a half after installation, operators report that there has been no damage to the belt and they are just now replacing some bars in the main impact zone. They report that downtime and labor due to maintenance on the loading zone has been drastically reduced, improving production and reducing the cost of operation. "We were impressed with the performance," said an operator close to the project. "The equipment and service exceeded our expectations." Following a successful performance testing phase, managers have installed MD Impact Cradles for 9 other conveyor loading zones of varying belt widths and sizes.