Lower costs and higher efficiency means more profits… we can help!
For recycling companies, changing economic conditions around the world are making it more and more difficult to turn a profit. It’s the law of supply and demand and, sure, as more and more consumers have gotten used to recycling household waste, the supply of paper, plastics, metal and glass has expanded. At the same time, however, fluctuations in currency and a cooling Chinese economy have reduced demand, squeezing revenues and profits.
While prices have dropped, the cost of processing recyclables hasn’t. In fact, for companies in sustainable materials management (formerly classified as “municipal waste” by the Environmental Protection Agency) the cost of the recycling equipment, manpower and energy required to move all that material has actually gone up because consumers are putting increasing amounts of non-recyclables – like plastic garbage bags – into the stream. This can clog up processing equipment, including conveyor belts and hoppers, and cause unexpected shutdowns.
High-quality, durable solutions that will improve your conveyor belt operation.
At Martin Engineering, we have a 80-year history of manufacturing high-quality equipment designed specifically to keep materials – like recyclables and waste – flowing efficiently. And because waste and recycling plants move large volumes of material that varies greatly, from household waste and organic byproducts to construction waste, your equipment has to accommodate a wide range of conditions. Whether your flow stream is being moved along by a conveyor system, into and out of a hopper or truck bed, or down a chute and through an unloading port, we have developed products that prevent obstructions from accumulating in turns and bottlenecks.
We are a global leader in providing flow aids like industrial vibrators and air cannons that keep material from sticking to the sides of containers and chutes and obstructing its movement through the process. Plus, we offer the most efficient belt cleaners on the market, eliminating the carryback that can travel with the belt back into the tail pulley and potentially damage your equipment.
Guaranteed to do the job… 100% no risk!
When you’re running on thin profit margins, the conveyor belt equipment you use absolutely has to work. Without fail! At Martin, we back all of our products and services with our 100% Money-Back Guarantee. That means if you’re not completely satisfied with the performance of any product, you can return it and we will refund your money no questions asked.
So pick up the phone and call one of our professional engineers or technicians. We enjoy talking shop and would love to hear about your operation, the challenges you face and what you’ve already tried as a solution. With the amount of experience we have under our belts, it’s pretty likely we’ve dealt with it before. And if not, we’re always up for a new challenge!
- Keep downtime for maintenance and housekeeping to a minimum
- Move recycled material more efficiently through the process
- Reduce spillage and equipment damage by keeping conveyor belts clean
- Prevent material from spilling off of moving conveyor belts
- Eliminate the need for workers to enter confined spaces
- Manage airborne dust and minimize the risk of inhalation and explosion
- Deliver more product by maximizing overall throughput
- Eliminate excessive downtime for conveyor belt maintenance and cleanup
- Reduce costs by minimizing waste and reducing energy consumption
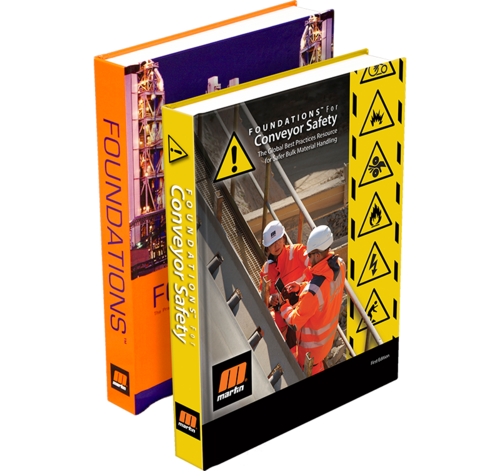
Foundations™ for Conveyor Safety
Learn to Calculate your Return on Conveyor Safety™ with our compilation of worldwide best practices for safer bulk material handling in this first-ever textbook dedicated exclusively to the safety of conveyor systems.
Request Your FREE PDF or Hard-Back Copy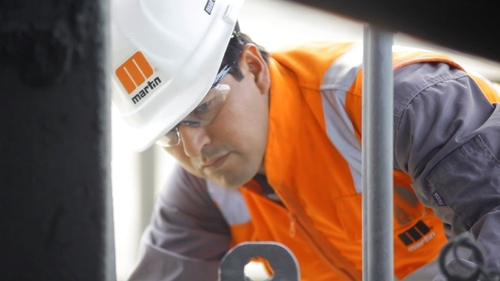
Save With Our Martin® Walk the Belt™ Service!
Every conveyor is different, even within the same facility! We can provide regularly-scheduled reviews of your bulk material handling system components, involving a specialized crew with the expertise necessary to achieve high operating standards, keeping the conveyor system running at maximum productivity. Immediate data and photos will be available to facility managers and our suggestions will ensure long-term savings and efficiency.
Get Your Belts Reviewed By People Who Know What They’re Looking At -- At No Charge!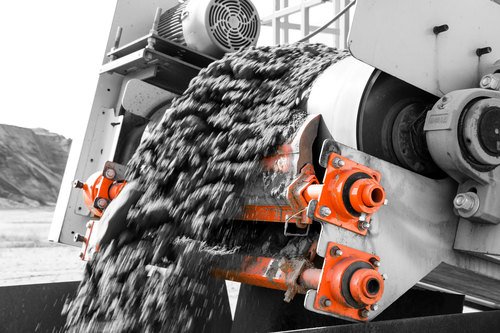
Martin® Forever Belt Cleaner Guarantee
We are so confident in the performance of our belt cleaners that we proudly offer the industry's first Forever Belt Cleaner Guarantee, an exclusive offer available for current genuine Martin® replacement blade customers. We will provide Martin® replacement tensioners and mainframes for any belt cleaner assemblies as required – whether the ones we're replacing were manufactured by us or not – absolutely free of charge for as long as we have a service relationship including FREE blade installation, tensioning and hardware upgrades, helping to maintain maximum performance and keeping your belt cleaning system running in like new condition – FOREVER!
Learn More About Our Guarantees Here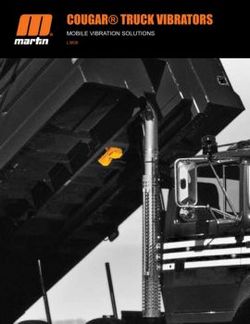
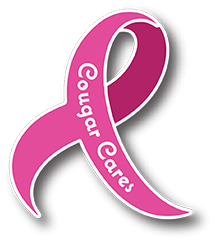
Cougar patented the world's first 12-volt truck vibrator in 1964. We continue to make the most rugged, reliable truck vibrators on the market.
For breast cancer awareness/research, we are donating $50 to Susan G. Komen Cancer Foundation for each limited-edition pink truck vibrator purchased during the month of October. CLICK HERE to learn more.